Contents
Cover
Concrete seat
$5.00- Pay online by credit card, debit card, or Paypal using Secure Server Paypal. You do not need a Paypal account if paying by credit or …
|
Preface
Concrete furniture for the garden certainly takes a lot of beating.
It pretty much fits in with any type of landscape design. This concrete seat is a little beaut. It is easy to make and inexpensive. In fact, most of the work and cost is in the making of the form (mold), however you only need to make the form once in order to make as many seats as you like.
Once you are set up and have made one seat, chances are you’re bound to make another.
And of course, a concrete seat is going to last a long, long time.
Introduction
This concrete seat is 32″ (800mm) long, 14″ (350mm) wide, and stands 14″ (350mm) high.
It is reinforced with wire mesh and weighs around 117 lb (53 kg).
Designing and writing about such a project is a lot more involved than simply making it for one’s self.
A lot of thought has to go into the design and the method of making, so it can be explained in a way that readers are able to understand.
Thought has to go into the easy availability of materials, along with terminology.
Also taken into consideration is the type of tools that the average DIYer is likely to own.
This particular project took four takes before it was ready to put to paper.
Maybe make a few to sell!
There is more expense and time in the making of the form (mold) for the concrete seat, than in making the actual concrete seat itself,
however you only need to make the form once in order to make multiple seats.
It makes good economical sense to make more than one seat after taking the trouble to make the form.
Not including the form, the cost of making each seat is inexpensive in relation to a similar type of seat made from wood.
You basically only need a wheelbarrow of concrete mix, some reinforcing mesh, and some release agent, all of which can be obtained quite cheaply – and even more so in bulk. Each seat takes but a couple of hours to make and gets easier with practice.
Maybe there could be a couple of bucks in making and selling the odd seat or two….just a thought.
About the measurements, Materials you will need and Informative notes
This project is in four parts
Part 1. Making the form (mold)
Part 2. Preparing the reinforcing mesh
Part 3. Making the concrete
Part 4. Casting the concrete
The four parts will guide you step-by-step through all the stages of making the form (mold), preparing the reinforcing, making the release agent, applying the release agent, making the concrete, pouring the concrete, settling the concrete, removing the form, and cleaning-up.
There is also a page giving easier options, albeit for a less exciting seat.
Note about the measurements
Dimensions given throughout this project are in both imperial (inches) and metric (mm). The imperial measurements are given first, followed by the metric measurements in brackets ( ). For example: 2″ x 4″ (100mm x 50mm).
Materials you will need
- 11ft (3.3m) of 2″ x 4″ (100mm x 50mm) wood, allowing for a little bit of waste.
- 4ft (1200mm) of 2½” x 5½” (140mm x 62mm) wood.
-OR-
- 13ft (3.9m) of ¾” x 5½” (140mm x 20mm) wood. * see Note 1
* Note 1: 2½” (62mm) thick wood is less common than ¾” (20mm) thick wood, and harder to cut the shape with a jig-saw (although it can be done). The ¾” (20mm) thick wood is more readily available and of course a lot easier to cut, but you will need three times as many pieces, as you will need to glue and screw three pieces together to make up for every one piece of the thicker wood. The thicker option is the best way to go if you can manage to acquire the wood (or close to it) and have the tools to cut it.
- 8ft (2400mm) of ½” (12mm) angle fillet, allowing for a little bit of waste. * see Note 2
* Note 2: Angle fillet is a triangular shaped strip of wood. Its purpose is to make a beveled-type edge around the top of the seat. You can use a different profiled piece of wood if you want something a bit more fanciful, or you can disregard it altogether for a plainer look.
- Half a standard sheet of ⅝” (15mm) thick plywood. A standard sheet is 4ft x 8ft (1200mm x 2400mm) so you will need half of that, allowing for a little bit of waste.
- 1 piece of ⅛” (3mm) thick plastic sheet, 40″ x 22″ (1000mm x 550mm). * see Note 3
* Note 3: The plastic sheet is to make a smooth finish on the top of the seat. The end product of a concrete cast will be as smooth as the form. The plastic sheet can be any thickness, or you can disregard it altogether, in which case the finished product will be as smooth as the plywood form. That can still be a reasonable finish.
Materials continued and cutting list for the form
Materials you will need, continued…
- 12 of 4⅜” (110mm) long x ⅜” (10mm) diameter hex bolts.
- 4 of 3½” (90mm) long x ⅜” (10mm) diameter coach/carriage bolts.
- 16 of ⅜” (10mm) wing nuts.
- 4 of ⅜” (10mm) standard nuts.
- 32 of ⅜” (10mm) round washers.
- 30 of 1½” (38mm) long wood screws and 12 of 1″ (25mm) long wood screws.
- 4 of 4″ x 2″ x 2″wide (100mm x 50mm x 50mm wide) galvanized angle brackets. * see Note 4
* Note 4: The angle brackets are to hold the leg form to the seat form. They make for easy alignment when it comes to assembling the form for casting. The bracket size given above is not absolute. Anything similar will do as long as it does the trick. You may have to make your own by cutting, bending, and drilling a piece of sheet metal. On the other hand, you can do away with them altogether and use clamps to hold the leg forms to the seat form. This latter method will require a bit of extra measuring and aligning when it comes to assembling the forms for casting.
- 5 sq ft (0.5 sq m) of 5/32″ (4mm) or slightly thicker reinforcing wire mesh. * see Note 5
* Note 5: Home-mixed concrete is not always as strong as it could be, so reinforcing steel or mesh is necessary. The mesh and method used in this project is but one way of adding adequate reinforcing. You can even make up your own grid using the same size or a thicker rod, and join the intersections with tie wire. The most important point is that the reinforcing covers the area of the seat and is also tied to other reinforcing that bends into the leg area.
- About three-quarters of the average heavy-duty wheelbarrow full of concrete mix (gravel, sand, and cement).
- And… some release agent so the concrete doesn’t stick to the form. * see Note 6
* Note 6: A release agent is a substance that is applied to surfaces to prevent them from sticking, in this case so that the concrete does not stick to the form. You can purchase form release agents from some building supply stores, often in handy little spray bottles. You can also make your own for a fraction of the price out of an even mixture of used car oil and diesel, and apply it with a paintbrush or a rag. That’s what we do.
The cutting list for the form
Plywood
ID | FOR | STOCK | SIZE | QTY |
[a] | seat top | ⅝” (15mm) thick plywood | 40″ x 22″ (1000mm x 550mm) | 1 |
[b] | leg sides | ⅝” (15mm) thick plywood | 17⅝” x 12″ (440mm x 300mm) | 4 |
Lumber/wood
ID | FOR | STOCK SIZE | LENGTH | QTY |
[c] | seat sides | 2″ x 4″ (100mm x 50mm) | 40″ (1000mm) | 2 |
[d] | seat ends | 2″ x 4″ (100mm x 50mm) | 22″ (550mm) | 2 |
[e] | leg fronts/backs | 2½” x 5½” (140mm x 62mm) * see Note 1. previous page for other size options | 12″ (300mm) | 4 |
[f]1 | around inside perimeter of seat form | ½” (12mm) angle fillet | 14″ (350mm) | 2 |
[f]2 | around inside perimeter of seat form | ½” (12mm) angle fillet | 32″ (800mm) | 2 |
The plans – dimensions
The form pieces
Cutting detail for pieces (e)
The form plans – schematic
Part 1. Making the form
The form is the mold or the boxing that holds the wet concrete in place until it sets.
Step 1.1 Cutting and assembling the frame pieces of the seat form
The two (c) pieces and the two (d) pieces are of 2″ x 4″ (100mm x 50mm) stock. They can all be cut from one 11ft (3.3m) length.
Before you cut the individual pieces to length, make a 10° angle cut (chamfer, bevel) along one edge of the wood, as shown in the drawing.
This is best done on a bench saw with the blade tilted 10 degrees.
With a certain amount of skill, it can also be done with a circular power saw with its blade tilted 10 degrees.
Then cut the two (c) pieces and the two (d)pieces to the dimensions given in the drawing below.
Note: The drawings below show the wider face of the wood. The beveled edge is the bottom (lower) edge of the pieces in the drawing.
Then, on a flat even surface, glue and nail or screw the (c) pieces and the (d) pieces together in picture-frame fashion.
Step 1.2 Cutting the plywood, the plastic, and assembling the seat form
Cut a rectangular piece of ⅝” (15mm) thick plywood, 40″ long x 22″ wide (1000mm long x 550mm wide).
Also cut a rectangular piece of ⅛” (3mm) thick *plastic sheet, 40″ long x 22″ wide (1000mm long x 550mm wide).
*Note: The plastic sheet is to make a smooth finish on the top of the seat. The end product of a concrete cast will be as smooth as the form. The plastic sheet can be any thickness, or you can disregard it altogether, in which case the finished product will be as smooth as the plywood form – which can still be an acceptable finish.
Lay the piece of plywood on a flat even surface.
Then lay the plastic sheet on top of the plywood sheet and the ‘picture frame’ on top of that.
Temporarily hold everything in place with clamps while you screw the all the pieces together.
Fix (glue and nail) strips of ½” (12mm) *angle fillet (f) around the inside perimeter of the seat form against the frame and the plastic sheet.
*Note: Angle fillet is a triangular shaped strip of wood. Its purpose is to make a beveled-type edge around the top of the seat. You can use a different profiled piece of wood if you want something a bit more fanciful, or you can disregard it altogether, for a plainer look.
Step 1.3 Cutting the form pieces for the legs
Cut 4 pieces (e) of *2½” x 5½” (140mm x 62mm) wood, at 12″ (300mm) long.
Each piece will need to be shaped.
Cut a piece of cardboard 5 ½” (140mm) wide x 12″ (300mm) long.
Draw a grid onto the cardboard with line spacings 1″ (25mm).
Then copy (draw) the shape as shown in the grid plan, onto the cardboard using the grid lines as reference points.
Cut out the shape on the cardboard and use that as a pattern to mark all the (e) pieces. They can then be cut using a jigsaw or other suitable tool.
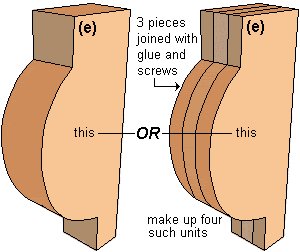
*Note: 2½” (62mm) thick wood is less common than ¾” (20mm) thick wood and harder to cut the shape with a jigsaw, although it can be done. ¾” (20mm) thick wood is more readily available and of course a lot easier to cut, but you will need three times as many pieces, as you will need to glue and screw three pieces together to make up for every one piece of the thicker wood. The thicker option is the best way to go if you can somehow acquire the wood (or close to it) and have the tools to cut it.
Next cut 4 pieces of ⅝” (15mm) thick plywood, 17⅝” long x 12″ wide (440mm long x 300mm wide).
Mark six hole positions on each piece. Refer to the drawing for hole positions.
Step 1.4 Assembling the forms for the legs
Sandwich the (e) pieces between the plywood (b) pieces.
Position the pieces in place (refer to the drawings on the previous page) and hold them there with clamps.
In all, there will be two leg forms, each consisting of two (e) pieces and two plywood (b) pieces.
The plywood (b) pieces are already marked for drilling. That was done in Step 1.3.
Drill through the leg forms on each drill mark.
Use a ½” (12mm) diameter drill-bit to drill the holes. The bolts are ⅜” (10mm) diameter. The bigger hole enables the bolts to be easily inserted and removed.
It is important to make the holes approximately ⅛” (2mm) bigger in diameter than the bolts to ensure that they (the bolts) can be removed easily when it’s time to release the form-work.
When the holes are drilled, you can then insert the galvanized ⅜” (10mm) hex bolts into the holes, add the washers, screw on the wing-nuts, and tighten.
Next screw a 4″ x 2″ x 2″wide (100mm x 50mm x 50mm wide) *galvanized angle bracket (or similar) to each end of each leg form. Four brackets in all.
Use only three screws to hold each bracket, as they will have to be unscrewed when it’s time to release the form-work.
*Note: The angle brackets are to hold the leg form to the seat form. They make for easy alignment when it comes to assembling the form for casting. The bracket size given above is not absolute. Anything similar will do as long as it does the trick. You may have to make your own by cutting, bending, and drilling a piece of sheet metal. On the other hand, you can do away with them altogether and use clamps to hold the leg forms to the seat form. The latter method however, will require a bit of extra measuring and aligning when it comes to assembling the forms for casting.
Step 1.5 Aligning and bolting the leg forms to the seat form
The purpose of this step is to allow for easy alignment of the leg forms over the seat form during the casting process.
The casting process involves half-filling up the seat form with concrete, placing in the reinforcing, filling the seat form with concrete, and fixing the leg forms in place ready for more concrete.
It is the latter stage that is made easier and quicker with the addition of the angle brackets.
Do this step in the following order:
Measure 4⅜” (110mm) along pieces (c) from the inside corners of the seat form and mark across pieces (c). See fig.1.
Place the leg forms against the mark. Ensure that the leg forms are equal distance from the sides. Mark the drill holes on pieces (c) through the holes in the angle brackets. (See fig.2.) Then remove the leg forms.
Drill down into pieces (c) to a depth of ½” (12mm) with a 1⅛” (28mm) diameter drill bit, and then continue the rest of the way through with a ½” (12mm) drill bit. (See fig.3.) There will be four holes in all.
Insert a ⅜” (10mm) coach/carriage bolt into each hole from underneath and secure each bolt with a washer and nut. The nuts will finish below the surface of the wood. See fig.3.
*Note: The angle brackets are to hold the leg form to the seat form. They make for easy alignment when it comes to assembling the form for casting. The bracket size given above is not absolute. Anything similar will do as long as it does the trick. You may have to make your own by cutting, bending, and drilling a piece of sheet metal. On the other hand, you can do away with them altogether and use clamps to hold the leg forms to the seat form. The latter method however, will require a bit of extra measuring and aligning when it comes to assembling the forms for casting.
Part 2. Preparing the reinforcing mesh
Steps 2.1 to 2.3 Cutting, shaping and tying the mesh
The reinforcing used in this project is *welded wire mesh. It is a grid of 5/32″ (4mm) thick wire with spacings at 6″ (150mm).
This reinforcing mesh and method is not the only way. Other material and methods can be applied. See the note at the bottom of this page.
Step 2.1 Cutting the mesh
Cut the mesh to the sizes given in fig.1. Cut one A piece and two B pieces.
The B pieces will have to be trimmed, bent, and shaped to suit.
Step 2.2 Shaping the mesh
Trim the two B pieces as shown in fig.1.
Bend the two B pieces 90° (right angles) along the bend line as shown in fig.1.
Pull in the sides where shown in fig.1 until they are approximately 4″ (100mm) apart.
Place the B pieces in a leg-form cavity to check that they fit. If not, make any necessary adjustments.
Step 2.3 Tying the mesh
Lay the A piece on a flat surface.
Tuck the shorter area of the B pieces underneath the A piece wire.
Position the B pieces so that the uprights (longer areas) are 19½” (488mm) apart (from center to center).
Then tie the B pieces to the A piece with tie wire (a thinner wire that bends easy).
*Note: Home-mixed concrete is not always as strong as it could be, so reinforcing steel or mesh is necessary. The mesh and method used in this project is but one way of adding adequate reinforcing. You can even make up your own grid using the same size or a thicker rod, and join the intersections with tie wire. The most important point is that the reinforcing covers the area of the seat and is also tied to other reinforcing that bends into the leg area.
Part 3. Making the concrete
Concrete mix information
This concrete seat will take about three-quarters of the average heavy-duty wheelbarrow full of concrete to make.
For this project we are going to make the concrete mix a little bit wetter than normal and add a slightly larger ratio of cement to the mix than usual. This will allow the concrete to get to every corner of the form without too much of a problem. If there is any ponding i.e. liquid puddles of sorts on top of the mix when finished (mixing), then it is too wet. If that is the case, mix in some more aggregate and cement. Likewise, if the mix is too dry, add water. The ready-to-pour mixture should be a good even, flowing consistency.
Three ingredients make the concrete: aggregate, cement, and water.
What’s aggregate?
Aggregate (in this sense and for this purpose) is a mixture of different size stones ranging from 20mm (¾”) diameter maximum, down to the size of a grain of sand. The smaller stones fill up the cavity created by the bigger stones.
You can make your own aggregate by mixing 3 parts gravel and 2 parts sand.
The mixture to make the concrete seat
The bucket
A standard household plastic 2 gallon (9 or 10 liter) bucket.
A. Aggregate
Four and a half buckets of aggregate.
B. Cement
One bucket of cement.
C. Water
Approximately ⅝ of a bucket of water. This can vary depending on the dryness or dampness of the aggregate.
Start with ½ a bucket and add more if needed.
Note: You can purchase concrete mix in handy bags from most building supply stores. The bags contain the aggregate and the cement already mixed, and only require the addition of water.
It is a more expensive way to go but usually more convenient for a one-off project.
Steps 3.1 to 3.2 Dry and wet mix
Step 3.1 The dry mix
Pour 4½ buckets of aggregate into the wheelbarrow and also 1 bucket of cement.
Give it a bit of a mix around with a spade.
Make a small crater in the top of the mix to take the water.
Note: aggregate is a mixture of different size stones ranging from 20mm (¾”) diameter maximum, down to the size of a grain of sand. The smaller stones fill up the cavity created by the bigger stones.
Step 3.2 The wet mix
Next add the water: approximately half a standard household bucket to begin with. Mix with the spade from underneath and fold over. Keep doing this and adding more water if required, until the mix is a uniform consistency.
Tip: when mixing, a smaller spade is easier to work with than a larger one.
Safety note: Prolonged contact with fresh concrete will burn your skin.
One mix will make one concrete seat.
Part 4. Casting the concrete
Steps 4.1 to 4.3 Applying the release agent, half filling the seat form and placing the reinforcing
Lay all the form pieces out on a flat work surface.
Step 4.1 Applying the release agent
Apply ample *release agent to all the form pieces on all sides with a paint brush.
Wipe off any excess with a rag.
*Note: A release agent is a substance that is applied to surfaces to prevent them from sticking, in this case so that the concrete does not stick to the form. You can purchase form release agents from some building supply stores, often in handy little spray bottles. You can also make your own for a fraction of the cost out of an even mixture of used car oil and diesel, and apply it with a paintbrush or a rag. That’s what we do.
Step 4.2 Half filling the seat form
Pack the seat form an inch or two up off the work surface so that you are able to get a hand under the ends. This is so you can lift an end up slightly and drop it multiple times in quick succession to vibrate and settle the concrete to help eliminate air pockets and make a smooth surface.
A little under half-fill the seat form with concrete and vibrate the form to settle the concrete. Do this by tamping and poking the concrete with a broad thin stick, say ⅛” (3mm) thick x 1½” (38mm) wide, also by using the rapid drop method as mentioned above, and also by tapping around the edge of the form with a hammer. The more vibrating the better.
Step 4.3 Placing the reinforcing
Sit the reinforcing on top of the settled concrete, in the center of the seat form. Remember, the seat form is a little under half full at this stage.
Steps 4.4 to 4.5 Topping up the seat form and attach the leg forms to the seat form
Step 4.4 Topping up the seat form
Top up the seat form with more concrete.
In fact, over-fill it, and then….
Rapity tapity tap
Vibration time. Bang around the sides of the form with a hammer.
Lift one end of the form up slightly and drop it. Do this multiple times in quick succession.
The more vibrating the better.
It settles the finer wetter mix around the coarser mix, gets rid of the air pocket holes, and makes the finished product a lot smoother.
Screed off the excess concrete.
Use a straight piece of wood to “screed” or level out the concrete.
Work the screed board back and forth with a sawing motion along the tops of the form until the concrete is level all over.
Step 4.5 Attach the leg forms to the seat form
Partially assemble each leg form, with one side panel (b) only, and place them in position on the seat form around the reinforcing wire.
Slipping the angle brackets over the bolts in the seat form will automatically place the leg forms in the right position.
Then add the second panel (b) to each leg form and fasten them in place with the wing-nuts.
Likewise, tighten the angle brackets to the seat form with wing-nuts.
Step 4.6 Topping up the leg forms
Start shoveling concrete into the leg forms.
But as you go….
More rapity tapity tap
As you go, tamp, poke, prod, with a broad stick – say a piece of plastic, steel, or wood about ⅛” (3mm) thick x 1½” (38mm) wide.
Do a lot of rapity tapity tap around the sides of the leg forms.
It would spoil an otherwise good job if the end product was full of air-pocket holes and gaps for the lack of a bit of rapity tapity tap
Once filled and settled, remove the excess concrete.
Have a bit of a clean-up
The next morning you can clean up a bit more.
All the splashed and spilled concrete should scrape off from the form easily enough if the form work was adequately coated with the release agent.
That’s pretty much it for a while.
Let it sit there for three or four days.
Let the concrete set (cure) slowly
The longer concrete takes to set (cure), the stronger it will be.
Keep the concrete shaded during the curing period.
Keep the concrete moist for at least a day or so by hosing with a fine mist every now and then. This is more crucial in warmer conditions.
The release agent, apart from just being a release agent, also serves another purpose. It prevents the moisture in the concrete from soaking into the form, thus helping to prevent the concrete from drying out too fast.
Step 4.7 Releasing the leg forms
Undo all the wing-nuts off the bolts on the sides of the leg forms.
Take out all the bolts.
The bolts should slip out easily, simply because the diameter of the bolt holes are bigger than the diameter of the bolts. The holes are ½” (12mm), the bolts are ⅜” (10mm). You did make the holes bigger, didn’t you?
The sides of the leg forms should come away quite easily.
This is when you get the first look at your handiwork, and you will find out if you did enough rapity tapity tap.
Remove only the first angle bracket. Do one at a time, so as not to get them mixed up (for possible future castings).
Once you have taken off the first angle bracket, you can then remove the respective piece (e), by nudging or tapping it out from the top.
When that piece (e) is off, immediately screw the angle bracket back to it.
By doing one at a time, i.e. taking off one angle bracket, removing the respective piece (e), and screwing back the angle bracket to the same piece it came off, then you are not going to get all the bits and pieces mixed up should you decide to make another seat.
Now remove the other three angle brackets and (e) pieces in the same manner, one set at a time.
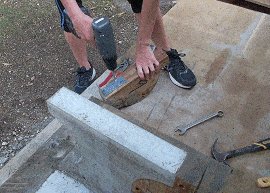
Step 4.8 Releasing the seat form
Slip a piece of board under the middle of the seat form.
Of course, you will need someone to tilt the seat back while you do that.
The board can be 1″ (25mm) thick more or less, it doesn’t really matter, and 20″ (500mm) long x 6″ (150mm) wide.
Stand on the two sides of the seat form and give a little bounce up and down.
This will break the seal between the concrete and the form. You will visibly see the seal breaking – a slight parting between the concrete and the form.
The seal will be more of a suction seal, rather than an adhesive seal, because of the release agent. Standing on the form and giving a little bounce will break that seal.
Now stand on the two ends (as opposed to the two sides) and do the same thing.
Now the concrete seat should easily lift out of the form.
If by any chance it does not, then turn the whole unit upright and knock one end of the seat form up by hitting it from underneath with a hammer.
You only need a little bit of air in to break any suction hold.
Mmmmmmm. Looks pretty good to me.
Appendage: Easier options
Easier options albeit for a less exciting seat.
Discard the angle fillets
You can do-away with the angle fillets for a plainer look around the top of the seat.
If you do-away with the angle fillets you must run the bevel cut on pieces (c) and (d) through the full thickness of the wood.
Discard the angle brackets
Use clamps instead of the brackets to hold the leg forms to the seat form.
You will save sourcing or making the brackets and fitting them, and also save from having to fix the connecting bolts to the seat form.
The downside is that without the brackets and by using clamps, you will have to manually measure and position the units as you go. Okay for a one of, but probably not much chop if you intend to make a few.
The brackets on the leg forms and the connecting bolts in the seat form make for a quick and accurate alignment when bringing them together during the casting process
Discard the fancy shaped (e) pieces
You can replace the fancy curved (e) pieces with straight pieces, say 2 ½” x 2 ½” (62mm x 62mm) stock or bigger.
This will save the time and effort of making the curved (e) pieces.
It will also save a little time during the casting process, as you will not have to dismantle the leg forms when positioning them around the reinforcing.
The downside is that the legs of the finished product will be straight, and pretty much characterless.
Discard the plastic sheet
The plastic sheet is to give a smooth finish to the top of the seat. You can do away with it and just use the plywood.
If the plywood surface is smooth, then so too will be the finish on the concrete (although probably not as smooth as with the plastic).
Concrete will take on the same finish as the form itself.
The legs on my concrete bench crumbled. do you know where I could purchase just the legs?